“Absolute quality” series automatically controlled filtration systems (UPF.A) are especially popular on distilleries and wineries at the stage of finish filtration before filling line.
“Absolute quality” filtration systems make the filtration process totally visible, reliable and cost effective to the whole enterprise. The customer is able to fully control filtration process and be sure of the quality of finishing product.
“Absolute quality” filtration systems are basically used in the food industry for beverage production and are intended for fine treatment and polishing of the product immediately before filling. Application of such filtration systems allows to exclude human component, avoid hydraulic shocks, save on wear parts and coordinate operation of separate production units.
The operation of standard filtration systems is based on a two-step filtration scheme. Depth filter elements with high dirt-holding capacity of the first stage perform the primary filtration and the filter elements of the second stage ensure the required quality of filtration.
Selection of filter elements depends on the kind of the beverage to be filtered. Specialists of Technofilter RME help you to choose the appropriate filtration system according to special requirements.
Standard filtration systems are designed for operation at the filling rate within the range from 0.5 to 12 m3/h.
Additional information about the “Absolute quality” filtration system is presented on a web-site vodka-tf.com.
Advantages of “Absolute quality” series filtration systems
- Automation unit ensures coordination of filtration system with filling line of any type (with a mechanical, solenoid or pneumatic valve). Frequency drive (proportional plus integral control law is applied for regulation) operating the pump motor maintains the constant downstream pressure specified by operator, generally 0.3 – 0.5 bar. In case the valve on the filling line reacts the pressure rise on the downstream of filtration system occurs. The pressure alarm comes from the gauge to the controller which in turn reduces pressure to set values. The operation procedure to avoid hydraulic shock is the “know-how” of Technofilter RME. The high speed of system respond on the pressure rise and the effective reducing of the hydraulic shock allows to install filtration systems in the filling lines with mechanical, pneumatic and solenoid valves. Moreover it ensures the safety and durability of high cost membrane and depth filter elements.
- Operator touch-screen panel enables to control all filtration parameters on-line. On the start screen such parameters as filtration rate (m3/h) and the degree of pollution (%) of filters on any filtration step. The possibility to control the operational life of filters (in liters) enables customer to choose filters with best compromise between price and quality.
- Automatic equipment ensures best performance conditions for the filter cartridges (smooth start and elimination of hydraulic shocks is ensured). Frequency drive on command from the controller enables smooth start of the pump. Gentle raise of the pressure enables the safety of filter elements.
- Automatic control of differential pressure at each filtration step precludes the possibility of filter mechanical destruction in the process of its contamination. Automatic control used in the filtration systems control the pressure drop on each filter. In case the pressure on a single filter exceeds the set value the filtration system stops and reports the necessity of filter exchange.
- Application of automatic equipment allows using a more powerful pump which ensures full development of the filter element operational life. When the pressure drop on a filter elements reaches the value of 2.5 bar this means that its operational life is expired. Therefore a more powerful plant is installed in the filtration system to enable filter element completely exhaust its service life.
- The filtration systems enable to wash filter elements from microfluff in a closed circuit.
- For memory retention of filters change-round date in the first and second filter holders the filters removal record is used.
- There is a possibility of liquid removal from filter holders in 1-2 minutes.
Functional capabilities
- Control system is based on reliable microcontroller by Siemens. Touch-screen panel is intended to visual control of parameters and system operation.
- Automatic system with PI – controller maintains the pre-set pressure value downstream the system.
- Solenoid valve is installed on the bypass line for effective reduction of hydraulic shock.
- The filtration system enables to effectively wash filter elements from microfluff in a closed circuit. The option of washing filter elements is used in preoperational phase before work and after filters change. Thus the time for start-up operations greatly shortens. Operating in washing mode the filtration system thereby discounts the possibility of microfluff insertion into the filling line (Microfluff usually enters the filling line at the moment of the filters change). Filtration systems operation practice proves the necessity of pre-wash procedure.
- The possibility of system automatic cut-off in case of filter exhausting is also provided.
- The filtration system is also equipped with dry running gauge.
- Microcontroller regularly fulfils self-checking.
Controlled parameters (presented on the touch-screen)
- Contamination degree (%) of filter element.
- The pressure at different filtration steps (bar).
- The throughput of filter elements (L).
- Filtration system capacity (m3/h).
Technical specification of standard “Absolute quality” UPF.A series filtration systems
System type |
UPF.А-2 (5х750/5х750)-3 |
UPF.А-2 (8х750/8х750)-6 |
UPF.А-2 (18х750/18х750)-12 |
---|---|---|---|
Nominal capacity (m3/h) |
3 |
6 |
12 |
Number of filtration steps (pcs) |
2 |
||
Power voltage (V)/ electrical power (kWt) |
3 х 380/1,5 |
||
Dimensions (mm), no more |
1750х850х1450 |
2100х1250х1600 |
2200х1200х1900 |
Weight, kg, no more |
110 |
150 |
250 |
Number of filter elements (pcs.) /adapter (mm) |
5+5/44,5 |
8+8/44,5 |
18+18/44,5 |
Filter element height, mm |
750 |
750 |
750 |
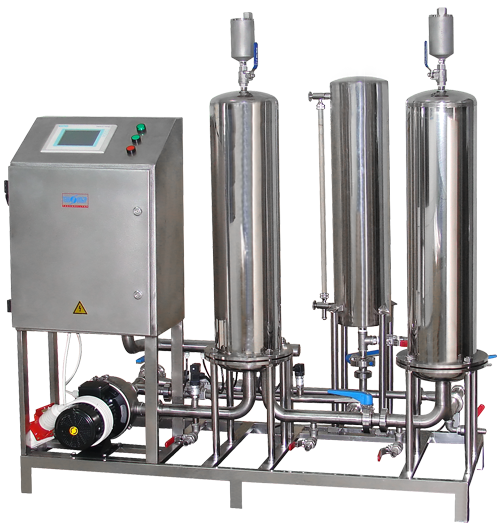
Completing units of standard two-unit filtration system UPF.A with 3 m3/h capacity
UPF.A is mounted on the frame and consists of:
- pump (GRUNDFOS, Germany);
- filtration unit (two stainless steel (12Х18Н10Т) filter holders DS-5-A-750P with highly polished surface for 5 filter elements 750 mm height coming with air separator);
- damping device, inverted solenoid valve;
- dry running gauge, filter element contamination level gauges;
- touch-screen control panel, frequency converter, piping, on-off valves.
Besides standard two-step filtration scheme there is possibility to adapt system to the individual customer’s requirements (three – and four-step filtration scheme).
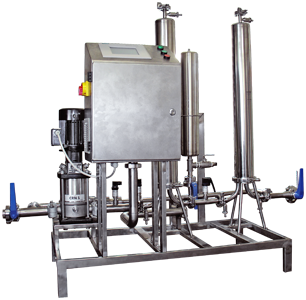
Options
On the basis of automatic polishing filtration system, systems with additional washing skid for filter elements regeneration using washing liquids and water as well as with air filter for displacement of filtered liquid from filter housings have been developed.
The washing skid allows the customer to regenerate filter elements without removing them from filter holders. Compressed air application significantly reduces time for filter element replacement.